Centrifugal Separators
Centrimax - Winkelhorst Trenntechnik GmbH supplies refurbished, but generally overhauled centrifugal separators made by GEA Westfalia Separator, Alfa Laval (Tetra Pak) and Flottweg for the centrifugal separation of solids and liquids.
Every centrifugal separator is subjected to a comprehensive general overhaul and subsequently delivered with a mechanical guarantee. Furthermore the separators are fitted with new PLC systems, with their help every separator can be integrated into the existing production process without any problems.
The scope of the Centrimax programme includes all the centrifugal separator types on the market (e.g. separators with automatic drum):
- Disc stack centrifuges with self-cleaning or with solid wall drum
- Nozzle separators
- Chamber separators with 2 chamber or 6 chamber insert
Areas of use for centrifugal separators
Centrifugal separators are high speed “liquid oriented” centrifuges (i.e. the solid material content may not exceed a defined portion) for the mechanical separation and be used for:
Purification of suspensions (solid-liquid separation).
- The purification separator, also known as purifier or 2 phase separator.
Separation of liquid mixtures (liquid-liquid separation).
- The fluids may not be soluble in each other and must have different densities. The purifier separator is also simply known as separator (GEA Westfalia Separator), purifier or concentrator (Alfa Laval) or also 3 phase separator (Flottweg).
- The objective of a purifier is to separate a light phase as purely as possible.
- For a concentrator a particularly pure heavy phase should be gained.
Purification and separation of solid material loaded liquid mixtures (solid-liquid-liquid separation).
For the respective, desired area of use the corresponding separators with a purification drum or separators with a separation drum are used. The particle size of the solid material to be spun off should (roughly simplified) be in the range of ca, 0.5 up to ca. 700µm.
The maximum allowable solid material content in the suspension depends on the type of drum used. If the separator is suitable for the desired technical process depends on further factors, such as, for example, the viscosity of the liquids to be separated.
Functional and constructional characteristics of centrifugal separators
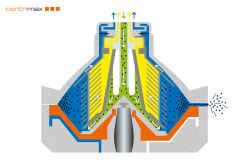
The Centrifugal separator belongs to the continuous sedimentation centrifuges with respect to the liquid discharge. With respect to the solid material discharge it can belong to discontinuous, the pseudo discontinuous or the continuous centrifuges depending on the design of the drum.
Centrifugal separators are vertically supported centrifuges. The feedstock is fed into the drum via a feed pipe (depending on the type of drum from the top or the bottom). The purified liquids or the liquids separated from each other are continuously discharged either pressure free or under pressure using an integrated pump. The solid material discharge can take place, depending on the design of the drum (chamber drum, solid walled disc drum), pseudo continuously (self-cleaning disc drum) or continuously (nozzle drum).
Centrifugal separator drum
The “centrepiece” of a centrifugal separator is the rotating so-called drum in which the actual separation process takes place. To enlarge the equivalent purification surface the drums can be equipped with certain fittings. With regard to the design of the drum, one can break down the centrifugal separators into the following:
Centrifugal Separators with disc drums (also known as disc stack centrifuges):
- with solid wall drum: discontinuous discharge of solid materials
- with self-cleaning drum: pseudo discontinuous (periodically) solid material discharge
- with nozzle drum (also known as nozzle separator): continuous solid material discharge
Centrifugal Separators with chamber drum (also known as chamber separators)
- with a 2 chamber insert: discontinuous (manual) solid material discharge
- with a 6 chamber insert: discontinuous (manual) solid material discharge
Centrifugal separator drive
As a rule the centrifugal separator is constructed exclusively as a vertical structure with flying bearings. The power transmission from the drive motor to the spindle (and thereby to the drum) can take place using helical gears, a belt drive or direct drive, via a special motor.
Sealing a centrifugal separator
Depending on the type of liquid feed to the centrifugal separator and the liquid discharge from the separator can be distinguished as open, semi-closed, hydrohermetic or fully hermetic separator.